The Best Guide To Alcast Company
Table of ContentsThe Only Guide to Alcast CompanyThe smart Trick of Alcast Company That Nobody is Talking AboutNot known Facts About Alcast Company10 Simple Techniques For Alcast CompanyThe Basic Principles Of Alcast Company An Unbiased View of Alcast Company
The subtle distinction depends on the chemical content. Chemical Contrast of Cast Light weight aluminum Alloys Silicon advertises castability by decreasing the alloy's melting temperature level and boosting fluidity during casting. It plays an essential function in enabling detailed molds to be filled accurately. Furthermore, silicon adds to the alloy's strength and put on resistance, making it beneficial in applications where longevity is important, such as auto parts and engine elements.It also enhances the machinability of the alloy, making it simpler to refine right into finished items. In this means, iron adds to the general workability of light weight aluminum alloys.
Manganese adds to the toughness of light weight aluminum alloys and enhances workability (aluminum metal casting). It is commonly utilized in wrought light weight aluminum items like sheets, extrusions, and profiles. The visibility of manganese help in the alloy's formability and resistance to splitting throughout fabrication procedures. Magnesium is a lightweight element that provides stamina and influence resistance to light weight aluminum alloys.
About Alcast Company
It permits the manufacturing of light-weight parts with exceptional mechanical buildings. Zinc boosts the castability of aluminum alloys and assists regulate the solidification process during spreading. It enhances the alloy's stamina and hardness. It is typically discovered in applications where elaborate forms and fine information are necessary, such as ornamental castings and specific vehicle parts.
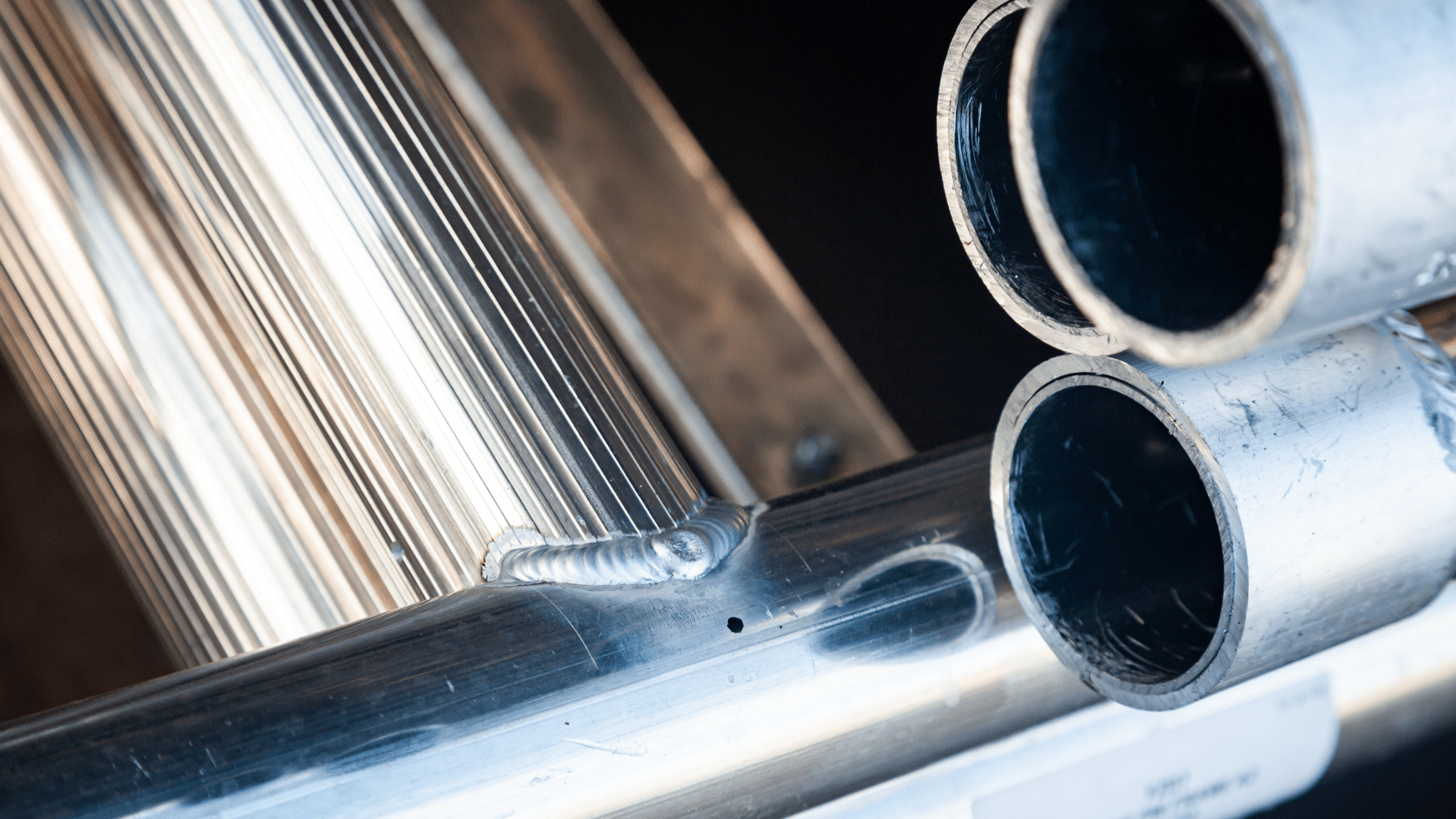
The key thermal conductivity, tensile strength, return strength, and prolongation vary. Select ideal basic materials according to the performance of the target product generated. Amongst the above alloys, A356 has the greatest thermal conductivity, and A380 and ADC12 have the least expensive. The tensile limitation is the opposite. A360 has the finest yield toughness and the highest possible prolongation price.
How Alcast Company can Save You Time, Stress, and Money.

In precision spreading, 6063 is fit for applications where elaborate geometries and high-quality surface area coatings are vital. Instances include telecommunication units, where the alloy's exceptional formability enables sleek and visually pleasing styles while keeping structural honesty. In a similar way, in the Illumination Solutions sector, precision-cast 6063 parts develop stylish and reliable lighting fixtures that require complex shapes and excellent thermal performance.
The A360 displays exceptional elongation, making it perfect for complex and thin-walled elements. In precision casting applications, A360 is fit for sectors such as Customer Electronics, Telecommunication, and Power Devices.
Alcast Company Fundamentals Explained
Its distinct residential properties make A360 an important choice for accuracy spreading in these industries, boosting product sturdiness and high quality. Aluminum alloy 380, or A380, is a widely used spreading alloy with a number of unique characteristics. It offers exceptional castability, making it an excellent selection for precision spreading. A380 exhibits good fluidity when molten, ensuring intricate and in-depth mold and mildews are properly reproduced.
In precision spreading, aluminum 413 beams in the Consumer Electronic Devices and Power Tools sectors. It's typically made use of to craft complex components like mobile phone housings, video camera bodies, and power device housings. Its accuracy is exceptional, with tight resistances up to 0.01 mm, ensuring remarkable product setting up. This alloy's superior rust resistance makes it an excellent choice for outside applications, making certain long-lasting, sturdy items in the mentioned markets.
A Biased View of Alcast Company
The aluminum alloy you select will significantly influence both the casting process and the properties of the last product. Since of this, you should make your choice carefully and take an enlightened approach.
Establishing the most appropriate light weight aluminum alloy for your application will mean weighing a vast array of attributes. The first category addresses alloy qualities that influence the production process.
Facts About Alcast Company Revealed
The alloy you choose for die casting straight affects numerous facets of the casting process, like exactly how simple the alloy is to collaborate with and if it is susceptible to casting issues. Warm cracking, also referred to as solidification splitting, is a regular die spreading problem for aluminum alloys that can cause inner or surface-level splits or fractures.
Certain aluminum alloys are much more susceptible to hot splitting than others, and your selection ought to consider this. An additional typical issue located in the die spreading of aluminum is die soldering, which is when the cast adheres to the die wall surfaces and makes ejection difficult. It see this site can damage both the actors and the die, so you ought to try to find alloys with high anti-soldering properties.
Rust resistance, which is currently a significant characteristic of aluminum, can vary considerably from alloy to alloy and is a necessary particular to think about depending upon the ecological problems your product will be subjected to (aluminum metal casting). Wear resistance is an additional building frequently looked for in aluminum products and can differentiate some alloys